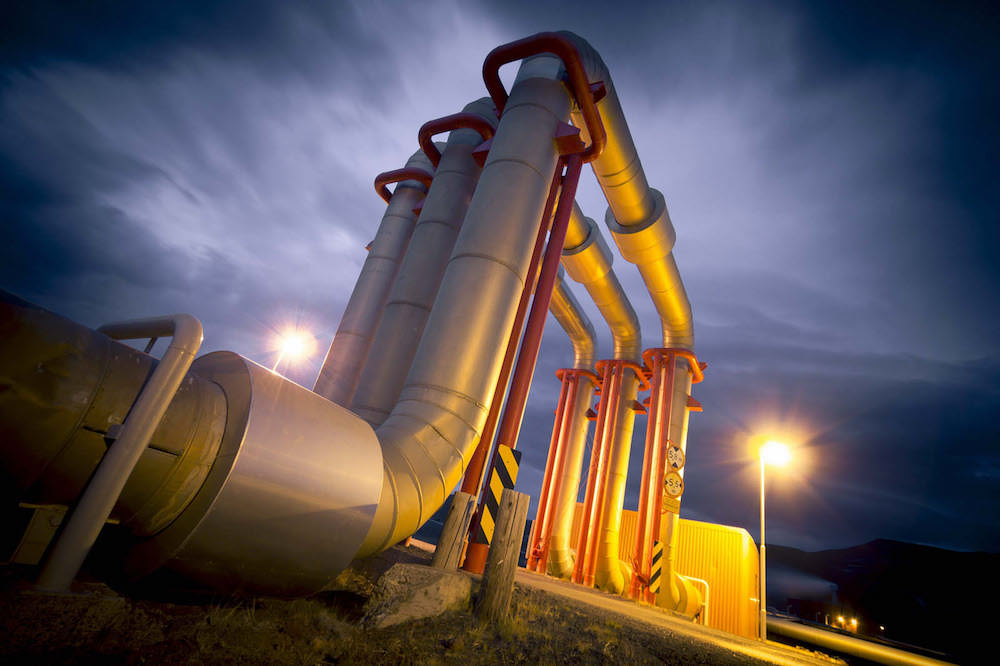
Matching valve type to function is a vital first step in the valve selection process. But how to choose the right ones for your need?
When selecting a valve for an instrumentation system, the choices can seem overwhelming. There are ball valves, diaphragm and bellows valves as well as check valves and excess flow valves, to name but a few each available in many sizes, configurations, materials, and actuation modes.
Matching valve type to function is the first and most important step in the valve selection process. Mismatches can be catastrophic. For example, if a ball valve were used in a high-pressure oxygen system, the sudden burst of oxygen enabled by the fast opening of the valve could lead to a fire if there were a source of ignition.
Packing in gate valves surrounds the cylindrical stem that connects the actuation with the inner mechanism preventing system media from escaping into the atmosphere where the stem meets the valve body. Valves with packing must be serviced or replaced at regular intervals, although some types of packing create more effective seals and last longer than others, such as the two-piece chevron design.
By contrast, diaphragm valves are packless and provide rapid shut-off and precise actuation speeds. Typically, diaphragm valves are employed in high-purity applications in the biopharmaceutical and semiconductor industries.
Each valve contains a thin metal or plastic diaphragm, which flexes up and down, creating a leak-tight seal over the inlet.Like the diaphragm valve, bellows valves are packless, making them a good choice when the seal to atmosphere is critical and access for maintenance is limited. Frequently, they are specified for the containment area in nuclear power plants.
The stem, which is entirely encased in a metal bellows, moves up and down (without rotating), sealing over the inlet.Flow-control valves enable the operator to increase or decrease flow by rotating the handle. The operator can adjust the valve to a desired flow rate, and the valve will hold that flow rate reliably. Common flow-control valves are needle, fine metering, and plug valves.
Needle valves provide excellent flow control and, depending on design, leak-tight shut-off. They consist of a long stem with a highly engineered stem-tip geometry (for example, veeor needle-shaped) that fits precisely into a seat over the inlet.You’ll need to give attention to installation issues, safety requirements and system parameters as well.
For the most precise flow control, however, fine metering valves should be considered. Typically found in laboratory settings, they have a fine stem that lowers through a long, narrow channel, ideal for marking fine gradations of flow.
Quarter-turn plug valves are economically priced utility valves. A quarter-turn actuation rotates a cylindrical plug in a straight-through flow path. The plug contains an orifice to permit flow. Plug valves are commonly used for low-pressure throttling applications.
For directional control over fluid flow, check valves or multi-ports should be considered. In check valves, the upstream fluid force pushes a spring-loaded poppet open, allowing flow.
In the case of an increase in downstream or back-pressure force, the poppet is forced back into the seat, stopping reverse flow. In most multi-port valves, fluid enters through a single inlet but may exit through one of many outlets, depending on the position of the actuator.
Excess flow valves stop uncontrolled release of system media if a downstream line ruptures. Under normal conditions, a spring holds a poppet in the open position. In an excess flow condition downstream, the poppet moves to a tripped position, stopping almost all fluid flow. When the system is corrected, the valve returns to its open position.
Once you have matched valve type to function, you are well on your way in the valve selection process. Many details remain, however. Ultimately, you will need to give attention to installation issues, maintenance schedules, safety requirements and system parameters, such as pressure, temperature, flow rates and system media.
https://www.theengineer.co.uk/issues/6-june-2011/selecting-the-right-valve/